Double Block and Bleed Valve
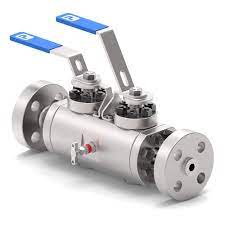
The increased activity in the offshore sector of the energy industry has led to additional factors that have to be taken into consideration when designing piping systems. Space in these modern locations is always at a premium and the design of piping systems and their associated components must therefore be more compact.
Features
Live Loaded Gland Packing
Antistatic Device
To ensure Electrical Continuity between the Stem and Ball and Body all Valves are provided with Antistatic device as an integral part of Floating Ball Valves.
Blow Out Proof Stem
Double ‘D’ Stem to Lever Connection
Equalized Cavity Pressure
Details
There are structural constraints that are also very important, such as keeping the structure as light as possible, and there are obvious benefits from making components smaller and lighter. Construction site job is also very expensive and any reduction in installation manpower is also beneficial. The above situation has led to the modification of the patterns of valve components to incorporate savings in space, weight, and labor costs where possible, while still retaining the original function of the valve.
The greatest savings are to be seen in the reduction of leak to atmosphere because the potential leak points are minimized compared to the conventional design. Process isolation philosophy has become more complex as safety issues have to be addressed and the requirement for double block and bleed isolation has become more commonly used. Double Block and Bleed isolation requires two in-line isolation valves and a bleed valve, used to drain or vent trapped fluid between the two closure elements
Design & Testing Standards
Design Standard:
- ASME B16.34
- API 6D
- BS -5351
- ISO 17292
- ISO 5211 (Mounting Pad)
End Connection Standards
- Face to Face : Manufactured & Standard
- Flange Dimensions : ASME B16.5, EN 1092 , JIS B 2220
- Butt weld End Dimensions : ASME B16.25,
- Socketweld End Dimensions : ASME B16.11
- Screwed End Dimensions : ASME B 16.11
Testing Standards
- Pressure Testing : API 598, API 6D, ASME/FCI 70.2, EN 12266-1, ISO 5208
- Fire Testing : API 607 / API 6FA
- Nace Requirements : MR 01-75
- Fuggitive Emission Testing : ISO 15848-2